Titanium Chemical Properties
The chemical element, titanium (Ti), has the atomic number 22 and an atomic weight of 47.90. It belongs to the first transition group and has a number of similarities with silica and zirconium. In lower oxidation states it has some similarities with chrome and vanadium as well.
When it is exposed to air at high temperatures, titanium metal and its alloys will oxidize immediately, forming a passive, but protective oxide coating. The same effect can be accomplished with nitrogen, which creates a coating of titanium nitride.
This protective oxide coating then serves to protect the metal from further oxidation, meaning that the first coat will appear quite readily, but anything that goes deeper will take a longer time.
Titanium is a thermodynamically reactive metal. It actually burns before the melting point is reached, which is why melting must be done in a vacuum or other inert atmosphere. By eliminating the oxygen, it is possible to heat it to the melting point without turning the metal to powder [12].
Titanium Alloys
Titanium alloys are grouped into four distinct types: commercially pure, alpha, beta, and alpha-beta. Each of these forms of the metal provides specific benefits, which means that different alloys will be used for different projects. Alloying elements are used to stabilize either the alpha or beta phase, which can create different characteristics to address different needs and to create titanium alloys that can be strengthened by heat treatment [13].
Commercially Pure Titanium – When titanium is not alloyed with any other metal, it is very ductile but has a lower strength. This makes it the preferred choice for applications in which corrosion resistance is a greater importance.
Alpha Alloys – These alloys are easy to weld and provide reliable strength at elevated temperatures. They are created with neutral alloying elements and alpha stabilizers, such as aluminum, but the results are not heat treatable.
Beta Alloys – These are the most common choices for projects that require higher tensile strength. A beta alloy is also heat treatable and contains sufficient beta stabilizers to maintain their beta phase even when quenched. Beta alloys use stabilizers like molybdenum or silicon, to create the desired characteristics.
Alpha-Beta Alloys – These are the most commonly used alloys because they combine the best characteristics of the other two alloys, creating a balance between strength, weight, and corrosion resistance. These alloys are heat treatable and are made with both alpha and beta stabilizers.
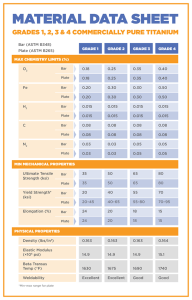
Unalloyed (Commercially Pure) Titanium Grades
CP titanium is graded on its corrosion resistance, formability, and strength. Unalloyed grades include 1 through 4, as wells as 7, 11, and 12. The higher the grade number, the higher the strength, however, the highest corrosion resistance and ductility is often found in the lower grade
Grade 1 (Ti 35A) – This grade has the highest formability and corrosion resistance but also has the lowest tensile strength
because of the low levels of iron and oxygen [14]. The most common forms for this grade are plate and tubing, and it is often used for chemical processing and marine applications.
Other jobs that will require a high resistance to corrosion, including food processing and pharmaceutical industries, bleaching or washing paper and pulp, medical tools and devices, anode and cathode cell components, desalinating various liquids, and consumer products utilize this grade on a regular basis.
Grade 2 (Ti 50A) – This is one of the most common grades of commercially pure titanium. It provides a good balance of strength, formability, and weldability. It has the same level of corrosion resistance as grade 1 titanium, but it is somewhat stronger [15]. It is commonly used in aerospace, marine, chemical, medical, and architectural applications such as:
- Chemical processing equipment
- Pollution control equipment
- Chemical processing equipment
- Medical devices and tools
- Consumer and recreational products
- Naval ship and aircraft components
- Power plant cooling systems
Grade 3 (Ti 65A) – While this grade has a very high tensile strength and corrosion resistance, it is one of the least used grades of pure titanium. It still has some uses in a number of major industries, such as the marine and chemical industries. It may also be used in power plant cooling systems, but other alloys seem to be a more popular choice [16].
Grade 4 (Ti 80A) – This is a very strong grade of titanium that possesses high levels of formability and weldability [13]. This is the grade for most medical titanium and is used for much of the surgical hardware in use. It also acts as a good heat exchanger and can be found in cryogenic vessels. Some of the more common applications include airframe and aircraft engine components, chemical processing machinery, heat exchangers, desalinization plants, and corrosive waste disposal equipment.
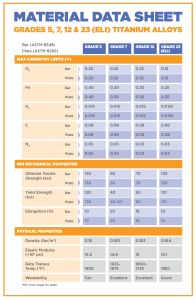
Alloyed Titanium Grades
Grade 5 (Ti 6Al-4V) – This is the most common grade of all the alloys and accounts for about half of the titanium used in the world. It can be heat treated to increase its strength, can be used at extremely high temperatures (up to 600F), and it has a good ductility. Titanium grade 5 is alloyed with 6% aluminum and 4% vanadium and is commonly used in aircrafts, automobiles, recreational equipment, and many other major industries.
This is simply the mostly widely used grade, and therefore it can be found in almost any industry that requires structural components with a high strength-to-weight ratio and corrosion resistance [19].
Grade 7 (Ti-0.15Pd) – This grade is commonly found in the chemical industry because of its high corrosion resistance. IT is mechanically and physically very similar to grade 2 titanium, but because palladium is present as an interstitial element, it receives other beneficial effects [18]. It has an excellent weldability rating, and offers a good level of strength and ductility. This makes it a valid choice for pollution control equipment, desalination equipment, hydrometallurgical extraction, paper and pulp bleaching and washing, chemical processing equipment, and anode and cathode cell components.
Grade 12 (Ti0.3Mo0.8Ni) – This alloy is very weldable and can be hot or cold formed with press brake forming, drop hammer, or stretch forming. It is often used in heat exchangers or in high temperature chemical applications, as well as marine and aerospace products because of the high level of heat resistance [20].
Other uses include anything where superior corrosion resistance in extreme temperatures is a concern, and it is used to make valves, pumps, pipes, fittings, and a range of other products.
Grade 23(Ti 6Al-4V ELI) – This grade is alloyed with the same metals as grade 5, but it is more pure and has a reduction of oxygen content. It has a good damage tolerance, and is often used in coils, wires, strands, but it is the choice material for various medical and dental applications. ELI grade titanium can resist damage better than other alloys (with high fracture toughness) and has better performance at cryogenic temperatures.
ELI titanium is used for medical implants because of its biocompatibility, osseointegration, good fatigue strength, light weight, and, most particularly, for its corrosion resistance. This is a result of the stable, continuous oxide film that immediately forms on the metal when it is exposed to oxygen. The human body is full of fluids that can corrode normal metals, making this characteristic extremely important [21].
While this is the choice metal for surgical implants and equipment, it is still often used in aircraft components, salt water equipment, cryogenic vessels, and other structural components [19].
Titanium Oxides
Titanium is normally coated with an oxide layer that usually renders it inactive and protects it from corrosive elements. When it first forms, it is only 1-2 nm thick, but it will continue to grow slowly. Titanium dioxide is actually the most commonly used titanium compound. It is used as a white pigment in paint, makeup, sunscreen, and a range of other products [4].
Applications across Multiple Industries
Aerospace – The aerospace industry has long understood the value of titanium. The industry is always looking for new ways to produce more fuel-efficient planes, and the strong, light-weight metal is an ideal choice. It brings the necessary structural reliability without the excess weight. Some estimates say that 72% of the titanium metal in the United States is used in aerospace construction [5].
Currently, titanium is used in the air frame and wing structures as well as smaller parts like compressor blades, rotors, stator blades, and other components of a turbine engine.
Titanium has several characteristics that make it particularly valuable in the aerospace market. First, the weight-to-strength ratio means that designers can create aircraft that are much more fuel efficient and a structural design that requires less interior space. Second, the natural corrosion resistance is particularly important under the galleys, which can be a very corrosive environment. Finally, titanium has very reliable thermal expansion rates, which is important when it is likely to be subjected to extreme variation on a single journey.
Automotive – Compared to aerospace, the automotive industry has not been as fast to adopt titanium as a major structural component. Even though the same beneficial characteristics (corrosion resistance, light weight, strong) apply, the consumer market (which is much more influential for automobiles than for aircraft) is very cost conscious, which limits the amount of titanium that is used in most vehicles.
Currently, most titanium is most commonly found in race cars or other specialty vehicles where weight and performance are critical, and the actual price is an afterthought.
However, titanium offers enough potential benefits that this is starting to change. The corrosion and heat resistance means that engine parts can last much longer, and the light weight materials mean it won’t have to work as hard. Now, as processing costs are starting to decline, there are more engines that use titanium for connecting rods, valves, springs, pins, and other components [2].
Marine – The corrosion resistance of titanium makes it a choice material for a wide variety of marine applications. Titanium can easily stand up to the corrosiveness of salt water, and research continues to determine who well it can handle steam, oil, and stack gasses, too [3].
Currently, titanium is used in water-jet inducers, sweater valve balls for submarines, fittings for yachts, propeller shafts, fire pumps, heat exchangers, and a range of piping and exhaust systems. If the components come into contact with sea water, opting for titanium is a good choice.
Medical – Since titanium does not react adversely to the human body, it is the choice metal for artificial hips, pins for setting bones, and dental or other biological implants. Every year, millions of pounds of titanium are implanted in patients because its properties lead to high osseointegration (the way bone integrates with the metal). Due to its non-corrosive characteristics, it will last for a long time in the body. Doctors won’t have to go in and perform a replacement a few years later [21].
Beyond bone and joint replacements, titanium is used for dental implants, cardiovascular devices (pacemakers), and surgical instruments. Medical grade titanium alloys also provide a better strength to weight ratio than other metals, such as stainless steel.
Recreational – The strength-to-weight ratio of titanium makes it a quality material for many different recreational products. Currently it is used in everything from bicycles to golf clubs. Due to the costs associated with milling and fabricating the products, they can be more expensive than similar products made of aluminum or steel, but many consumers are willing to pay the increased prices for higher quality.